I'm going to say this up front, for those of you who are just skimming or just want to look at the pretty pictures, for all the descriptions and detail I go into about the processes, etc. of finishing, when it comes to sound: thin finish = better.
So, why go into any of the following? Because, how do you know one finish from the next? AND, if you do know how to tell or what to ask, the reasons why some of the stuff is the way it is, is weird.
Before I begin talking about finish, I should probably talk a little bit about the physics of a guitar's sound. We know that an acoustic guitar makes sound by amplifying the plucked string. The sound of the string itself is amplified by the big hollow body. There are many factors, including finish, that goes into the quality, quantity and length of that sound.
Electric guitars are a bit more difficult. They are amplified by magnetic pickups. The movement of the string creates a signal that is run to an amplifier. So, we're technically not amplifying the string "sound" but rather the disturbance of the magnetic field.
The amount the string vibrates particularly influences the guitar tone, resonance and sustain in both electric and acoustic guitars. So, why is this important? Well, the finish of the guitar can directly effect the string vibrations and the resonance of the wood. Hence thin finish = better ... generally.
There are many, many, many, many different types of guitar finishes and systems. I'm going to cover some of the more popular and generic versions as most the others are variations of these. I'm not covering these chronologically, but rather Cullenlogically, which is to say with lack of logical progression but with method of madness.
Click images for full-size images.
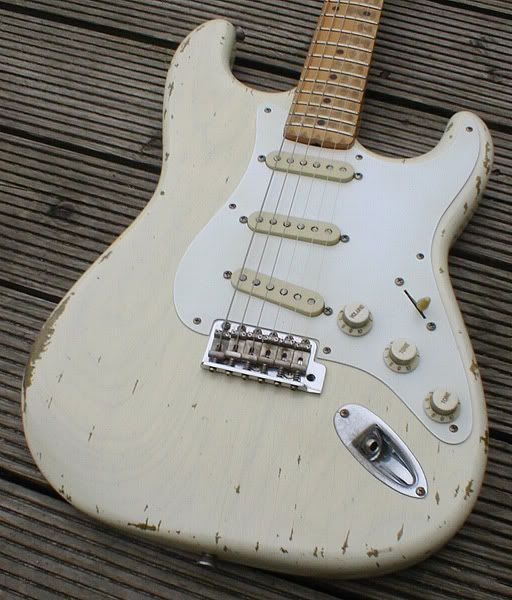

The advantages are that polyester finishes are very tough. They last a long time and look good for a long time. The bad thing is, as I hinted at above, this thicker finish dampens sound. The thick finish doesn't allow the wood and therefore, the strings, to vibrate as well as thinner finishes. Tone is dampened, sustain is cut. BUT, if you're playing hard rock or metal, this isn't very important. You're playing off the tone of your pickups and amp more anyway. However, if you're playing jazz or blues, you should be very concerned about this.
On acoustics, you can imagine that these finishes would more directly effect the sound. You would be right. If you're shopping acoustics, I would avoid any that has a solid color paint job.
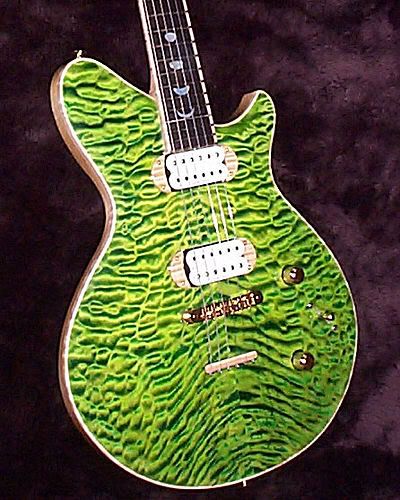
For buyers of electrics there are ways to tell if the guitar you're looking at has a polyester or nitro finish. First, if you're picking it up off the rack and it has a name on it that you recognize, you should automatically assume it has a polyester finish. You can ask the salesperson for documentation. You can also ask the salesperson to take off one of the strap buttons. Look at the hole where the button is screwed to the guitar. If you see a thick layer of paint and finish, it's poly. If there's hardly any noticeable distance between finish and wood, it's either a really good poly job or it's nitro. But, the big thing to keep in mind here is that you should play the instruments through the kind of amplification you have/want to have and see for yourself. Regardless of if it's poly or nitro, there are plenty of good-sounding guitars using both finishes. Experiment.

Advantages: An oil finish, like tung oil or even Miniwax Antique Finishes are actually a shellac-based oil finish. They don't block the pores of the wood thereby allowing the instrument to sing. It also feels most natural and your hand doesn't get stuck on a gunky neck like on highly finished necks. Oil finishes can be colored to warm up certain woods. Oil finishes are easy to apply.
Disadvantages: Oil finishes don't last very long. You have to reapply finish every so often - depending on how often it's handled. Also, while protecting the wood from the oils and dirt on your hands and arms, it doesn't protect the wood from scratches and dings from playing. If your guitar is made from a softer wood like Alder or Basswood, it's not a good idea to have an oil finish as it will get dinged up quickly. While this may be an advantage to some, to others it's a turn off - the finish doesn't get nice and shiny like a nitro or poly finish does. You'll always have a dull, "satin" finish.

Very accomplished French polishers will color different shellacs to create different burst effects. The practical upshot of this process is that it creates a beautiful, durable finish that is very light. Giving you a finish that rivals a nitro with nearly the amazing clarity of an oil finish. Of course, such labor don't come cheap. You can expect to pay hundreds if not thousands more for an instrument that has a French polish. Ed Roman ("bargain" high-end pricing) offers a French polish finish on his Quicksilver guitars for $350. I consider that a bargain.
-----------------
I hope you enjoyed this look into the world of guitar finishes. I barely scratched the surface. I didn't go into the different dyes or how one finish "burns" into its previous layers or how another finish layers on top of itself. I didn't talk about buffing or drying or applying or environmental considerations. What I hope I did is whet your appetite to find out more information.
If you do want to learn more, please visit the Musical Instrument Maker's Forum. If you register (it's free!), you have access to their library and TONS of information about building your own guitar, or maybe just touching up one that you already own.
No comments:
Post a Comment